The professional production and marketing of wood chips is not a business for the sidelines. Mathias Schneider is one of the contractors who has adapted perfectly to it. He knows that efficiency counts in this business. Since mid-2020, his chipper has been powered by a Fendt 942 Vario. I'm on the road in southern Germany - about 25 km northeast of Augsburg, to be precise. That's where the Schneider contracting company is based in Sainbach. I park my car on a meticulously tidy company site and am greeted warmly by LU Mathias Schneider, his wife Anna and his employee Josef Müller. Since 1998, the contracting company has already been involved in woodchip services. "From the beginning, we have produced wood chips with the tractor-chipper team. This concept suits us best," explains Mathias Schneider, adding, "We are on the road a lot in the field and in the forest. The access roads are often not suitable for trucks. But with the tractor-trailer combination, I can always get to the job site - no matter what time of year it is. After all, we also have to get out in the winter when the roads are covered in snow."
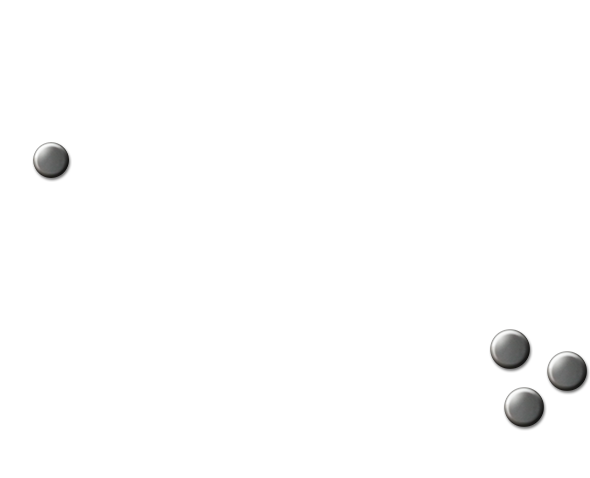
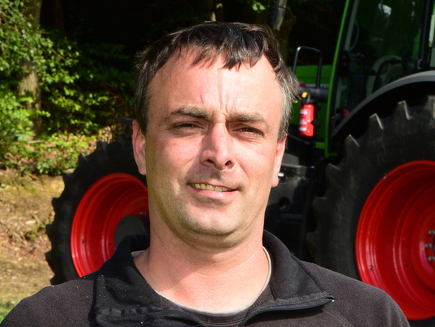
The 415 hp from the MAN engine with 9 l displacement, coupled with the low-speed concept, are optimal for chipper use.
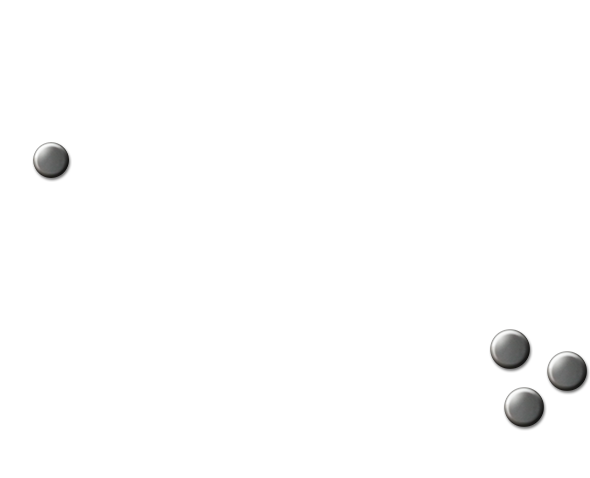
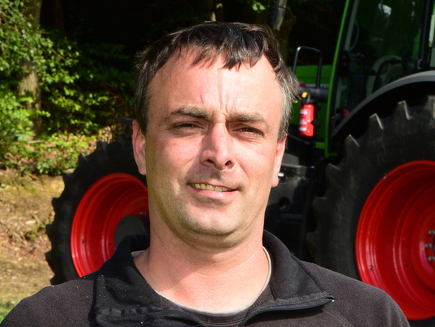
The 415 hp from the MAN engine with 9 l displacement, coupled with the low-speed concept, are optimal for chipper use.